and How Long It Can Maintain This Position? The automotive industry in Europe and North America faces significant challenges due to its underestimation of the electric vehicle (EV) revolution. Meanwhile, China, which has been focusing on a radical transformation of the sector for years, could emerge as the ultimate winner in the global competition.
According to South Korean SNE Research, over 10 million pure electric vehicles (BEVs) were sold worldwide last year. Including an additional 4.2 million plug-in hybrids (PHEVs), this figure exceeds the forecast from six months earlier by over 300,000 units. Current models, despite challenges such as fluctuating energy prices, intense competition, governmental policies, and infrastructure gaps, predict the sale of 16.75 million “plug-in cars” in 2024. Chinese manufacturers are expected to account for nearly 10 million of these sales, one million more than last year. This anticipated growth alone covers a third of last year’s electric car sales in Europe. Official data shows that 1,538,621 new BEVs were sold across the EU’s 27 member states in 2023, marking a 37% increase from 2022. This brings the total number of pure electric vehicles in the EU to approximately 4.7 million. Chinese electric cars are just beginning to appear in EU statistics, with the MG4 EV—a model from the formerly British brand MG, breaking into the top ten list of January sales.
The driving force behind the new automotive revolution is battery manufacturing. The battery is the heart of new vehicle designs, determining their performance and durability while accounting for 40% of manufacturing costs. In hindsight, the European and North American automotive industries made a significant mistake in the early 2010s by not taking the arrival of electric cars seriously and failing to recognize that battery manufacturing capabilities would shape the sector’s future. Few anticipated that battery production would reach a cost level that could challenge the oil industry. As Akshat Rathi points out in his recent book “Climate Capitalism” (Greystone Books, 2023), Bloomberg’s green economy reporter analyzed the connections between Japanese, South Korean, and Chinese battery manufacturing. He concluded that China developed and implemented its plans in a timely manner, giving it an advantage over its competitors. Those who can reliably supply many strong, quickly rechargeable, and lightweight battery cells to car manufacturers will dominate the market, potentially claiming the entire industry.
Battery Evolution and the Nobel Prize
The essential function of a battery is to convert chemical energy into electrical energy. This invention, which is 225 years old this year, is credited to Italian Alessandro Volta, who built the first galvanic cell. Sixty years later, Gaston Planté developed the first rechargeable battery. The French physicist’s lead-acid battery has modern descendants that have conquered the world. In the late 19th century, it even seemed for a moment that electric vehicles might dominate the nascent automotive industry. However, the electric cars produced by Gustave Trouvé in 1881 and the Flocken Elektrowagen in 1888, along with the approximately 30,000 electric cars on the roads at the turn of the century, quickly lost out to combustion engines. The lithium-ion battery, which ultimately challenged the dominance of petroleum products in the automotive industry, had yet to be invented.
This pivotal technology, which brings the end of the fossil fuel era into view, was born out of the oil industry. During the 1970s oil crisis, companies seeking alternative energy sources led to Stanley Whittingham at Exxon developing the first rechargeable lithium-ion battery. Despite its superior performance, lighter weight, greater moldability, durability, safety, and higher capacity compared to earlier generations, the design was shelved. The significance of Whittingham’s foundational research was later recognized, and he was awarded the Nobel Prize in 2019. This recognition was partly due to Sony’s popularization of Li-ion batteries in 1992 with its Handycam cameras. These batteries were subsequently integrated into household electronics, mobile phones, and more, with continuous improvements in capacity and production cost reductions. The industry-standard 18650 cell, a 3.6-volt “large pencil battery,” had a capacity of 1100 milliampere-hours (mAh) and cost over ten dollars to produce in 1994. Today, the capacity can reach 3500 mAh, with manufacturers guaranteeing over 500 life cycles, and production costs well below three dollars. This development paved the way for the global dominance of CATL, China’s leading automotive battery manufacturer.
The predecessor of the world’s largest battery cell manufacturer, ATL (Amperex Technology Limited), capitalized on the insatiable demand for smartphone batteries. Initially supplying batteries to Samsung and Apple, the company evolved when a subsidiary, CATL (Contemporary Amperex Technology Limited), was spun off in 2011. The “C” in CATL signifies its focus on manufacturing Li-ion batteries for electric vehicles (EVs). A significant challenge at the time was the shift from traditional galvanic cells, which involved standard-sized batteries connected in series or parallel, to more flexible cell structures tailored for EVs. For electric vehicles, however, technical and safety considerations necessitated battery cell structures that could be better and more efficiently adapted and molded to fit the shapes and designs of the models.
BMW provided the most valuable automotive experience in the Chinese market for this purpose. In 2013, when the Bavarians’ Chinese partner, Brilliance, launched the Zinoro based on the X1, CATL’s batteries were designed and integrated into the electric version. This partnership paved the way for CATL’s first European factory, built in Thuringia (D) by BMW’s Chinese suppliers, with plans in Debrecen (HU) following the same direction. At this time, the Chinese government elevated the requirement that battery packs in the increasingly important automotive industry be domestically produced into a strategic priority. The government supported the electric vehicle industry not only through incentives for purchasing and using electric vehicles but also by providing direct incentives to manufacturers since at least 2009.
In the latter half of the previous decade, Beijing placed companies manufacturing batteries for electric vehicles on a “white list,” offering strong state support to the entire sector. This facilitated rapid development, enabling manufacturers to produce critical components (such as cathodes, anodes, separators, and electrolytes) to increasingly higher standards. The significant subsidies eliminated competitive pressure from direct rivals in Japan and South Korea. There was also a high governmental tolerance for environmental pollution: stringent environmental regulations, if they existed, were not strictly enforced in practice. More important was establishing a complete value chain from mining to material research, development, production, final assembly, and recycling—ensuring that everything was Chinese, or at least under Chinese supervision. A prime example of this is that despite China already controlling 40 percent of the global cobalt reserves, it secured favorable strategic partnerships with major resource holders like Australia, Canada, and African countries.
China has the largest share
The 13th Five-Year Plan for the period 2016-2020, set by the Chinese Communist Party for the country, already includes a focus on industrial investments in battery production and control over the supply chains of electric vehicles, including critical rare earth mineral control. The importance of this is recognized not only by the Chinese. In the spring of 2021, the International Energy Agency (IEA) released a report on the role of critical minerals in clean energy production, stating that since the mineral demand for electric vehicle manufacturing could be six times that of fossil fuel vehicles, ownership of critical minerals and their deposits will be crucial due to increasing demand. According to a recent study by the Berlin-based Mercator Institute for China Studies (Merics), China now sets the pace because it has secured the largest market share. Approximately 70 percent of global battery manufacturing capacity is now located in China, and China is also a global powerhouse in seven key minerals (copper, lithium, nickel, manganese, cobalt, graphite, zinc) necessary for electric vehicle production. At the end of last year, SNE Research released the top 10 list of the world’s battery manufacturing capacity: six Chinese companies are on this list, with CATL and BYD leading. These two companies already provided more than half (55.2 percent) of the global demand for batteries in electric vehicles by January 2024.
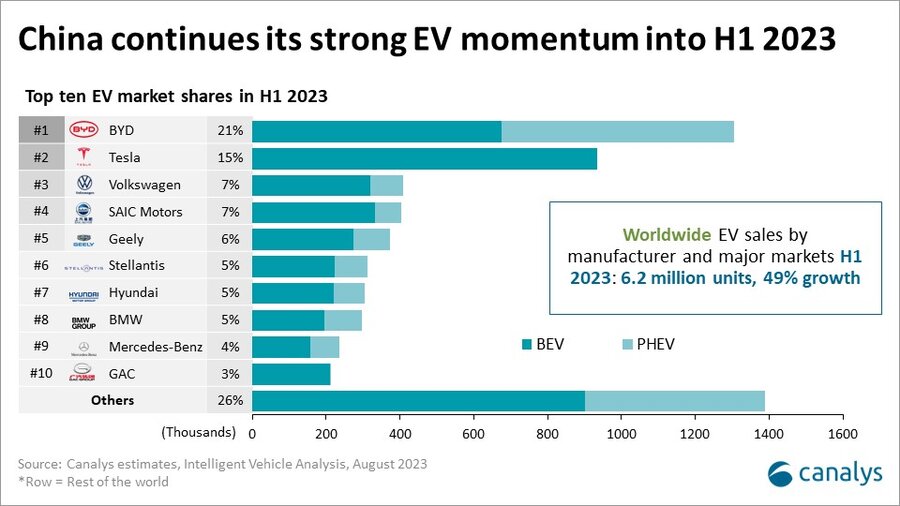
A leading official at Chinese Gotion High-tech, which collaborates with Volkswagen and ABB, recently explained the Chinese market dominance this way: if someone wanted to build a modern battery factory today, they would find everything they need within half an hour at companies operating in the Yangtze River Delta—the necessary raw materials and all semi-finished goods (from electrode materials to insulation foils to packaging). This concentration provides significant business advantages: Bloomberg calculated that the Chinese can undercut general manufacturing costs by 24 percent in the American market and up to 33 percent in the European market.
According to the latest estimates from Bloomberg’s investor advisory platform, BNEF, by 2025, China’s battery manufacturing capacity will triple that of the rest of the world. Currently, neither the United States nor the European Union can catch up with China. “In Europe, Tesla is pressing from the left, and BYD and other Chinese companies from the right,” explained Péter Kaderják, Executive Director of the Hungarian Battery Association. However, the battery industry has become the most dynamically growing sector precisely because “Europe has decided that the green transition must take place.” The strongest trend in this is the green energy transition, “which has not only led to political but also corporate decisions, shaping the direction of future investments and developments,” Kaderják added. According to the expert, who has also influenced Hungarian energy policy in the past, it is crucial that car manufacturers do not invest their money in developing internal combustion engines but in some zero-emission solutions—whether they like it or not. “The green transition means that we are essentially trying to replace all fossil fuels with clean electricity. However, this cannot work without new types of large-scale and everyday energy storage technologies and solutions.”
Currently, the vast majority of battery production is focused on meeting the needs of the automotive industry, which accounts for about 90 percent of manufacturing capacity—everything else falls into the remaining 10 percent. Although the expansion of manufacturing capacities realizes a very bold scenario, according to industry analysts, these proportions are unlikely to change significantly for a long time. But the limits of growth are not visible either in car manufacturing or in the network and residential energy storage market.
Canada, the Secret Contender
A few months ago, the most read Chinese-language newspaper in Singapore, Lianhe Zaobao, sought to answer whether China had won the global competition in battery production. The conditional answer was yes: according to the newspaper, although the ascent to the throne had happened, China should not be satisfied because the situation could change rapidly. Examining secure, reliable, and sustainable Li-ion battery supply chains, a report released by BNEF in February revealed surprising results: the list ranking 30 countries annually was no longer led by China. While BNEF analysts still considered China to have the strongest established supply chain, Canada emerged above the former leader in manufacturing and ESG (Environmental, Social, and Governance) development areas. If this trend persists, the pace of the transition in the US automotive industry will not depend on China. Another consequence of this dethronement is more political in nature: Chinese batteries could be the victims of Sino-American tensions—similarly to how Americans sank Huawei in the field of ICT.
The first victim has already emerged. After the Biden administration announced a plan last year that half of American cars would be electric by 2030, and a national network of 500,000 EV chargers was planned, in December last year, an idea was made public to keep foreign-owned companies away from this market. The concept, which was ultimately enshrined in the Bipartisan Infrastructure Law, makes it impossible for Chinese companies to enter the supply chain of the US electric vehicle market. Ford is already feeling the pinch: the law derailed a deal it had made with CATL last February, under which the Chinese company would have built a complete battery plant in Michigan—thus helping Ford, which was lagging behind in the evolving market, reduce its disadvantage. The project was halted last fall.
Turning Point on its way
A recent article in the Financial Times, based on internal industry information, concluded that the order of who leads in development competition could reverse in the coming years. Japanese automakers (Toyota, Honda, Nissan), who are currently seriously lagging behind, expect to take the lead in battery production with the arrival of solid-state batteries, considered the next milestone, overtaking Chinese CATL and BYD. “Toyota promises that by 2027/2028, with the new generation of energy storage systems, the batteries will provide electric cars with a range of 1200 kilometers, and they can be charged in ten minutes. In the fierce innovation race, VW also appeared alongside Honda and Nissan. The Germans joined an American development, enlisting the help of artificial intelligence (AI) and Microsoft. (VW’s own battery specialist company, PowerCo, has been collaborating with QuantumScape, a start-up, since 2012, becoming its main shareholder by investing $100 million in 2018 and another $200 million in 2020.) The essence of the development referred to with the promising phrase “changing the course of the game” is that AI enables faster and more accurate material tests, leading to cheaper new batteries. Experimental constructions are analyzed not in months or years but in weeks or even days, allowing more than 32 million materials, alloys, compounds to be examined within a foreseeable timeframe, ultimately resulting in better (cheaper, stronger, faster charging, etc.) batteries. However, mass production is still far off, even though in January, PowerCo announced that the sample cells performed very well in the Salzgitter laboratory.
China, therefore, is not showing signs of alarm. “According to the current five-year plan, a breakthrough in battery production and energy storage must be achieved—making this area ‘the Chinese powerhouse of science and technology.'” “CATL and BYD are reallocating significant resources to the development and construction of electric vehicle charging networks and the development of battery energy storage systems (BESS) for industrial and utility-scale needs. Battery production is mainly focused on meeting the needs of the automotive industry, which ties up about 90 percent of manufacturing capacity. However, China has recognized the threat lurking in solid-state technology and is preparing to change the current power balance. Although they intend to maintain the advantage they have gained, Beijing aims to establish a supply chain for solid-state batteries by 2030. To this end, they have established the China All-Solid-State Battery Collaborative Innovation Platform (CASIP), with the goal of developing and mass-producing solid-state batteries capable of competing globally under central control between science and industry (including CATL and BYD)—for the entire world’s automotive industry. CATL—just casually in April 2023—announced that they are ready to mass-produce sodium and lithium-cell hybrid battery packs, and the location of production has also been named—but since then, there has been no news of such energy storage devices being installed in cars.
In the background, however, something else has begun to take shape. After Xi Jinping declared in 2021 that China would achieve carbon neutrality by 2060, Goldman Sachs priced this promise. They estimated that by 2040, this would generate an investment commitment of roughly $7 trillion in energy infrastructure in the Asian country. In October last year, an Oxford analysis revealed that China’s energy storage sector had undergone a drastic transformation. The Tamarindo report stated that after the share of pump storage (PS) power plants among renewables in the Chinese electricity market fell below 80 percent in 2022, it further decreased to below 70 percent last year. China operates the world’s largest PS power plant capacity (45.7 gigawatts in 2022); thus, the change in ratio indicates that alongside PS, “everything else” in energy storage technology (Li-ion batteries, lead-acid batteries, flow energy storage, flywheels, compressed air, and gravitational energy storage) has also seen rapid growth. According to Goldman Sachs’ forecast, China will need at least 520 gigawatts of energy storage capacity—which is seventy times the amount in operation in 2021. Experts estimate that three-quarters of the newly installed capacity could come from batteries. While no scenario has been published yet, a company statistic has already revealed that in a short time, more than a hundred companies specializing in energy storage have emerged in the Chinese economy.